Detention and Hurricane Season
Hurricane season is not yet over and stormwater detention is top priority for most rebuilding communities. Billions of dollars of damage have been caused by flooding across our nation with the deadly combination of extreme rain events and too much concrete. Detention ponds cannot keep up with the combination of the rain deluge, overflowing bayous and rivers, overwhelmed stormwater systems and the increased runoff from impervious cover from ever expanding developments.
There is a solution that may save many homes and business from flooding. It is an actionable construction method that will save money, enhance aesthetics and most importantly add cumulative detention capacity to help combat large flood events. Add stormwater detention in every new development or redevelopment project with permeable pavers. Paving with permeable plastic grid pavers filled with gravel or grass is the new standard to add detention without adding cost. Furthermore, plastic grid permeable pavers provide opportunity for detention under the paving and is coded as 100 % pervious cover enabling developers and planners to utilize 100% of their land. The TRUEGRID permeable paver system is the permeable paving alternative to concrete and asphalt that can be used for commercial, industrial or residential paving applications including parking lots, storage facilities, bus pens, truck yards, fire lanes, and even driveways. The pavement system is 100% permeable and rain flows through system surface at over 800 inches per hour. Under the grid system a clean rock base serves as a detention pond so effectively you can drive on the surface and store stormwater below.
Plastic grid pavers can vary but the best system has a combination of rigidity and compression strength married with flexural design elements to handle any soil or climate. The grid has over 8000 psi compression strength when filled with gravel. This compares to most concrete paving at 5000psi. Commercial and industrial traffic including fully 18 wheelers can drive on the grid surface without issues such as cracking and potholes found in cement and asphalt. More importantly, under the plastic grid system in the base rock stormwater can be detained in 40% void space between the rock. Most cities and counties recognize this detention opportunity and code 100% pervious cover and 40% storm water detention volume capacity in the installation cross section of base rock and filled grid. A typical coded detention capacity for a plastic grid system with gravel fill and clean angular 57 stone sub-base is 8 to 9 inches per city code.
The traditional method of storm water detention involves digging and construction a detention pond or separate detention area to handle runoff from hardscape and impervious surfaces such as concrete or asphalt parking lots, roadways and of course, buildings. There are many negatives to this methodology. First up is the land use. Instead of utilizing this land for revenue generating purposes, i.e. additional buildings or parking or commercial space, the land now must be used to build a hole in the ground that will need costly construction as well as long term and continuous maintenance. Often in commercial developments as much as 25 % of the land on a site can be required for detention putting a large burden on the remaining usable property. Separate detention ponds can pose safety issues such as drowning hazards. If not maintained frequently the ponds become toxic and breeding grounds for disease carrying mosquitoes.
Putting detention capacity under plastic grid parking surface– drive on surface, detain storm water below- eliminates all these issues. And it performs for the life of the project, 25 to 40 years, virtually without maintenance.
The aesthetic can be important as the cost. Does anyone ever say – “boy I wish we had more concrete paving area!” Not unless they are concrete salesmen. The fact is that concrete is coming up in the conversation from city planners, engineers, architects and residents who are tired of flooding in heavy rain events due to runoff from concrete from over-development. Grass or gravel filled plastic grid with detention underneath results in some beautifully landscaped, natural elements or sites in what would otherwise be an unsightly concrete lot, fire lane or overgrown detention pond. The gravel color and texture can be chosen to fit in with the building and area. Grass filled plastic grid pavers can be used in applications such as fire lanes to and provide detention capacity underneath and act as French drain or a moat or sorts to keep water away from buildings and directed where the designers intend for the water to flow.
This permeable plastic grid paving methodology mimics nature in terms of stormwater management and the way in which rain water is absorbed, detained and released. Natural aquifers are recharged slowly with stormwater that has been filtered free of pollutants such as phosphorous, nitrogen and hydrocarbons by the bioremediation process and the natural microbial action of water flowing into and through the rock and soil before groundwater recharge. Contrast this to heavily polluted runoff from concrete and asphalt. The recent floods form Hurricane Harvey were a huge health hazard to rescuers and residents who had to wade through the toxic runoff.
A site to be developed is prepared by determining the amount of water detention capacity is needed on the site and the impact of the development on the site and the surrounding area. The depth of the excavation- be it six inches or three feet- is calculated over the square footage of the paving. The square footage multiplied by the depth and 40% void space when clean, washed, free of fines base rock is used determines the storage capacity in the cross section. The subgrade is cleared and leveled. A permeable filter fabric is placed between subgrade soil and the sub-base rock to keep separation and maintain capacity in the void space of the rock by preventing intermingling of the soil and rock base. In areas with porous subgrades, stormwater infiltration will occur into the soil through the fabric. In areas with fat clays or solid rock subgrades water will not infiltrate very much. In either instance the site subgrade may be directionally sloped to direct stormwater release slowly. Alternatively, perforated pipe or other drainage elements can be used to collect and channel the detained water towards the city storm water system or other outlet. The key is the detention to increase absorption and slow water movement and release over time so that heavy flash flooding does not occur and damage and endanger property and people.
If every paved developed site in a community – from driveways to strip centers and shopping malls to churches and parks to storage yards to every parking lot you can think of, the list is endless- was paved with permeable plastic grid pavers with detention capacity under the surface the results of heavy rain storms would be less tragic. This methodology mimics nature in terms of stormwater management and the way water is absorbed, detained and released. Natural aquifers are recharged slowly with stormwater that has been filtered free of pollutants such as phosphorous, nitrogen and hydrocarbons by the bioremediation process and the natural microbial action of water flowing into and through the rock and soil before groundwater recharge. Contrast this to heavily polluted runoff from concrete and asphalt. The recent floods form Hurricane Harvey were a huge health hazard to rescuers and residents who had to wade through the toxic runoff. How many homes with six inches or a foot of water have been saved or could be saved from flooding in the next big storm if much of the paving in the city could absorb and detain heavy rains like a sponge soaking up the overflow.
Development is a good thing when done wisely. Over-development with too much concrete and too little planning is not. Stormwater detention planning and low impact development with permeable grid pavers is the way to design and develop responsibly.
Listen in as Home Cents Live radio show host Mike Landry interviews TRUEGRID® Founder and CEO Barry Stiles about the benefits of TRUEGRID Permeable pavers and how they can help eliminate the need to build detention ponds. Mike also talks to preferred TRUEGRID contractor Brian Brown and his experience with the product.
Learn more about TRUEGRID® projects or products.
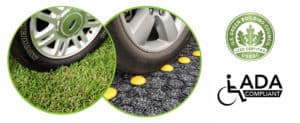
Providing accessible and convenient parking for customers is a necessity for any business—from small, family-owned restaurants and stores to the largest commercial retailers. Building a new parking lot can be an expensive proposition, especially when factors like proper drainage systems and long-term maintenance are considered.
Traditional paving materials, like concrete and asphalt, can be expensive to install and require plenty of maintenance as they age. In comparison, permeable pavers initially tend to cost significantly less than concrete, and although they are cost competitive to asphalt paving systems, permeable pavers don’t require the expensive drainage systems or significant long-term maintenance that asphalt does.
Here are five ways permeable pavers can help your business reduce parking lot design costs:
Permeable Paver Cost
1) Lower Material Costs
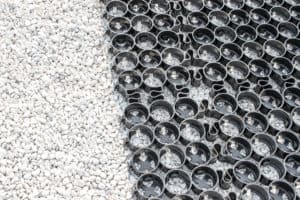
Permeable pavers use a combination of interlocking grids that are laid over a prepared subsurface and one of several fill materials, such as gravel or crushed limestone. Once the fill material is compacted into the grids, it creates a strong, durable parking surface that is virtually maintenance free.
Between the grids and the fill material, the cost of materials tends to be far less than concrete and similar to asphalt. Additionally, because the fill materials are acquired locally, shipping costs are greatly reduced compared to the price of transporting asphalt or concrete materials to the site.
2) Reduced Labor Costs
To install an asphalt parking surface, a large team is needed to run the paving equipment, transport the materials, and finish the surface. With concrete surfaces, a similarly large team is needed to transport the materials, erect forms, pour the concrete, and finish the surface. In both cases, the crews must be experienced and knowledgeable in order to do the job properly, and combined with the long installation times that are required for each surface, this leads to high labor costs.
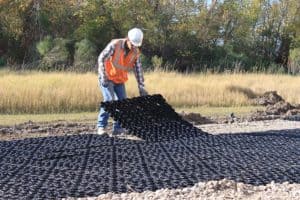
With permeable pavers, the installation process is quick and easy. After a suitable subsurface is created from compacted rock or limestone, the individual paving grids are laid over the surface and locked into place. Because the grids are extremely lightweight and cover a large area, the process goes very quickly. Afterward, the fill material can be spread, installed, and compacted by heavy equipment, such as a wheel loader. Overall, the installation process is much faster, and it requires fewer skilled laborers, reducing overall labor costs compared to concrete or asphalt installations.
3) Reduced Equipment Costs
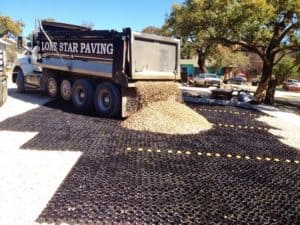
Anytime specialized equipment is required, such as paving machines, concrete trucks or rollers, the price of the job can increase significantly. Companies often charge over a hundred dollars an hour per piece of heavy equipment, which adds up quickly. With asphalt paving, there are several pieces of heavy equipment involved, including pavers, rollers, dump trucks, and more, depending on the job. Concrete installations require several concrete trucks, and they occasionally require pump trucks and smaller equipment. Such equipment increases the installation costs.
With permeable pavers, the amount of equipment is minimized.
Often the same dump trucks and loaders that installed the subsurface can be used to acquire and install the fill materials. Because less specialized equipment and fewer operators are required, the installation costs for permeable pavers tend to be lower than concrete or asphalt.
4) Reduced Maintenance Costs
Asphalt and concrete surfaces need a way to divert and control stormwater during inclement weather to avoid flooding the parking lot, eroding the surface, polluting nearby areas with runoff, or causing erosion of the soil in the surrounding areas. In order to control the runoff during storms, a large and expensive drain system must be built below the parking surface. This drain system would need to include storm drains, a system of pipes, and connections to either a municipal wastewater system or a detention pool. Not only does this increase the initial cost of the installation, but the required ongoing maintenance of the drain system also increases the long-term costs of the parking surface.
Permeable pavers feature a porous surface, which allows precipitation to naturally drain through to the subsurface. This stops the parking lot from flooding during heavy rain. It also produces less runoff that can erode the surface of the parking lot or nearby soil and carry pollutants into surrou
nding areas. This allows the water to refill the local aquifers naturally, and it requires no ongoing maintenance as standard drain systems do. By eliminating the drain system completely, permeable pavers cost significantly less to install and maintain.
5) Lower Long-Term Costs
Asphalt surfaces are extremely soft, especially during hot weather, and can easily crack or develop potholes. Overtime, the sealant also degrades, allowing the surface to erode away quicker. To keep an asphalt parking surface in good condition, any holes or cracks need to be filled periodically, and the entire surface must be resealed often.
Concrete surfaces are also prone to cracking and upheaval, especially in areas where frost occurs. Additionally, like asphalt, the surface also needs periodic resealing to avoid erosion. To repair cracks or other damage in concrete surfaces, the damaged areas must be removed or ground down and new cement or concrete must be poured to create a smooth surface. And, finally, both concrete and asphalt systems must have the drain system periodically cleaned to avoid clogs, as well as have any leaking pipes or damaged drains replaced. This ongoing maintenance significantly increases the long-term costs of concrete or asphalt paving systems.
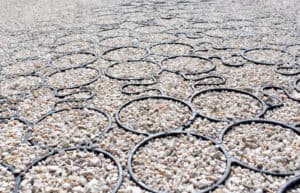
Permeable pavers create a strong, durable parking surface that has a similar lifespan to concrete or asphalt surfaces, but because the surface is flexible and porous and the fill material is securely contained within the interlocking grids, a parking surface made from permeable pavers requires very little ongoing maintenance, which reduces long-term costs.
Benefits of Permeable Pavers
Permeable pavers are a cost-effective, low-maintenance alternative to both concrete and asphalt surfaces, and with their porous design, locally sourced fill materials, and lightweight design made from recycled plastics, they are also environmentally-friendly and can help your project qualify for LEED certification.
Sources: